Too complicated: Some manufacturing processes entail too many details, making manual labour a simpler option.
MANUFACTURERS have been put in the spotlight in recent months as the call for automation grows ever stronger and the task of obtaining foreign workers become ever more challenging.
Manufacturers have expressed growing interest in automation and adopting new technology. But Corlite Packaging Industries Sdn Bhd managing director Toh Pe Kun points out that it really is not that easy.
Already a subscriber? Log in.
Limited time offer:
Just RM5 per month.
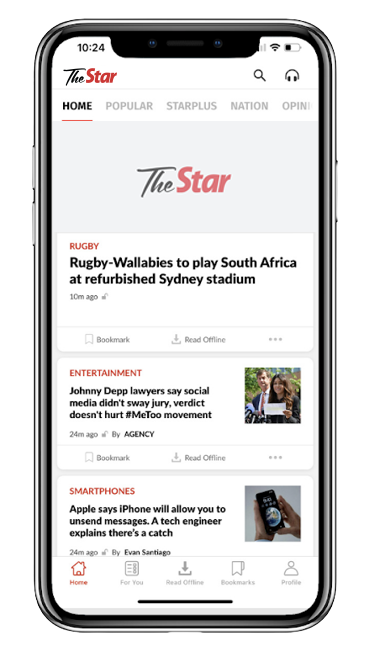
Cancel anytime. No ads. Auto-renewal. Unlimited access to the web and app. Personalised features. Members rewards.
Follow us on our official WhatsApp channel for breaking news alerts and key updates!