Unprepared: Local producers are far from ready to embrace Industry 4.0 as they are bogged down by cost, lack of skills and limited market access.
Mindset change important for manufacturers to adopt Industry 4.0 technologies
INDUSTRY 4.0 is the buzzword of the day. The government, and the industry alike, are talking about the technological transformation that will change the face of manufacturing in Malaysia.
Already a subscriber? Log in.
Limited time offer:
Just RM5 per month.
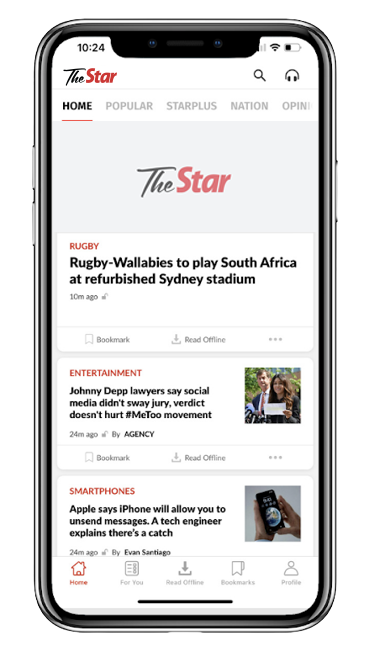
Cancel anytime. No ads. Auto-renewal. Unlimited access to the web and app. Personalised features. Members rewards.
Follow us on our official WhatsApp channel for breaking news alerts and key updates!