New product: Goh demonstrating the use of the advanced rotary dishwasher at its plant in Perai.
Companies keeping up with consumer demands for environmentally-friendly goods
WITH the business environment getting tough, due mainly to shortage of skilled workers and the slow down in some industries, some local SMEs are turning to producing environmentally-friendly products to stay competitive in the market.
Already a subscriber? Log in.
Limited time offer:
Just RM5 per month.
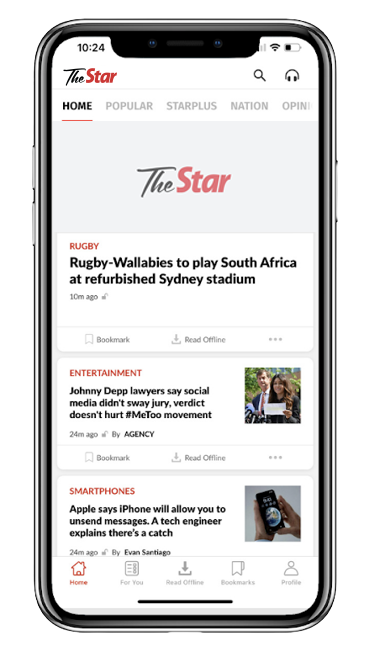
Cancel anytime. No ads. Auto-renewal. Unlimited access to the web and app. Personalised features. Members rewards.
Follow us on our official WhatsApp channel for breaking news alerts and key updates!