Token of appreciation: Country Garden Pacificview (CGPV) CEO Su Baiyuan (second from left) presenting a souvenir to Tee after the opening ceremony for the Forest City Industrialised Building System (IBS) manufacturing plant at Gelang Patah. Looking on are Country Garden Holdings CEO Mo Bin (left) and Mohd Othman.
GELANG PATAH: In response to the nation’s call for a green and smart construction industry, Country Garden Pacificview Sdn Bhd (CPGV) – the master developer of Forest City, launched its Industrialised Building System (IBS) base with a projected cost of RM2.6bil.
The entire base would span 168.7 ha and is said to be the largest of its kind in the world.
Limited time offer:
Just RM5 per month.
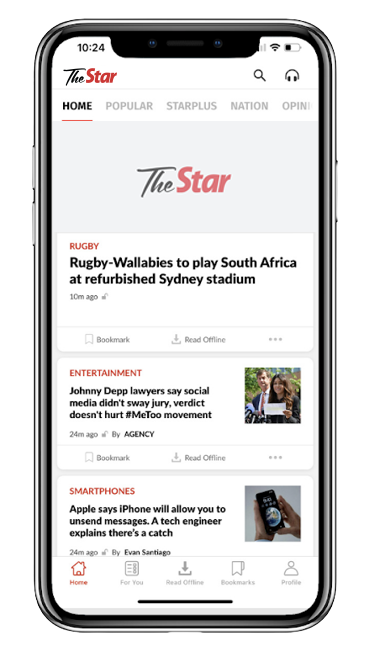