IF you need proof that the pace of globalisation has accelerated over the past decade and a half, look no further than the rising influence of FIFA, the international football association.
Operating in 204 countries, FIFA's reach is matched only by such noteworthy institutions as the Catholic Church and the United Nations, each having a presence in 202 and 191 nations respectively.
Already a subscriber? Log in.
Limited time offer:
Just RM5 per month.
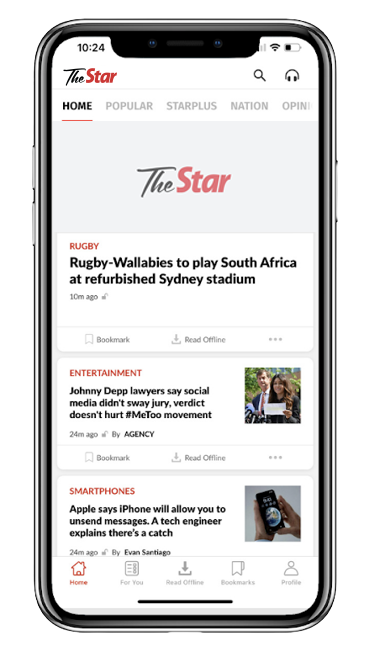
Cancel anytime. No ads. Auto-renewal. Unlimited access to the web and app. Personalised features. Members rewards.
Follow us on our official WhatsApp channel for breaking news alerts and key updates!