THE secret of Toyota's success is its tested production system, which emphasises efficiency and non-wastage. It basically consists of two techniques: kaizen or continual improvement, and “just in time” production.
In kaizen, Toyota is constantly looking for ways to improve production and lower costs.
Already a subscriber? Log in.
Limited time offer:
Just RM5 per month.
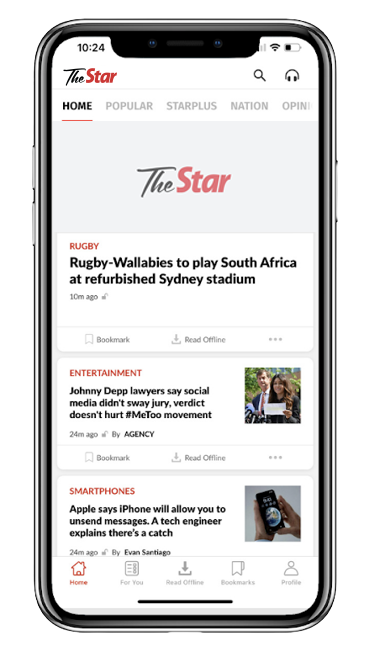
Cancel anytime. No ads. Auto-renewal. Unlimited access to the web and app. Personalised features. Members rewards.
Follow us on our official WhatsApp channel for breaking news alerts and key updates!