pic MUSTAFA AHMAD / The Star / 05 April 2016.
Penang-based company expects RM50mil increase in revenue this year from its recycle and waste management businesses, and sees more growth as it expands into recycling electronic waste from households and not just industries.
SHAN Poornam Sdn Bhd, a leading Penang-based waste management company in the country, aims to achieve RM250mil revenue for 2016, a 15% increase from RM200mil a year ago.
Already a subscriber? Log in.
Celebrate Merdeka with 50% Off!
T&C applies.
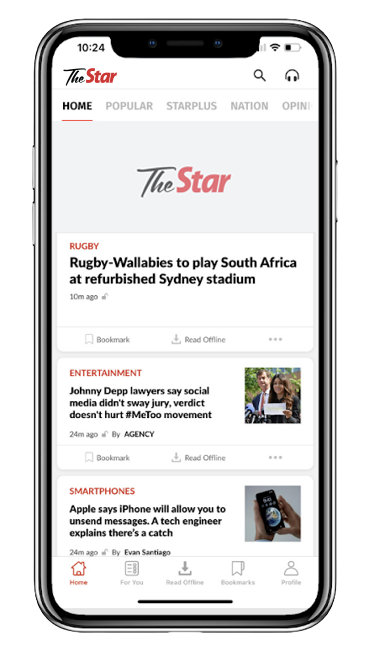
Cancel anytime. No ads. Auto-renewal. Unlimited access to the web and app. Personalised features. Members rewards.
Follow us on our official WhatsApp channel for breaking news alerts and key updates!