Kumar has gone on to CNC machining which enables more precise designs such as this neck-knife.
KNIFE-making, whether as a hobby or full-time job, can be very rewarding, especially when one sees his or her smithing or designs reaching new levels of mastery.
StarMetro talks to two people, one a skilled hobbyist and the other a professional knifemaker, on what got them interested in turning pieces of metal into well-crafted tools for the outdoors, kitchen or tactical use.
Already a subscriber? Log in.
Limited time offer:
Just RM5 per month.
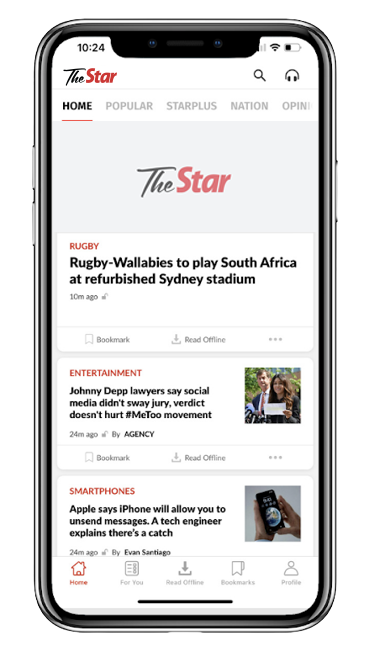
Cancel anytime. No ads. Auto-renewal. Unlimited access to the web and app. Personalised features. Members rewards.
Follow us on our official WhatsApp channel for breaking news alerts and key updates!