WHEN THE price of gold hit its all time high of over US$1,800 (RM5,800) an ounce in 2011, Time magazine reported that about US$130,000 worth of scrap gold was recovered from electronic waste retrieved from around 100,000 used phones alone.
Unfortunately, not all waste has similar economic value.
Already a subscriber? Log in.
Limited time offer:
Just RM5 per month.
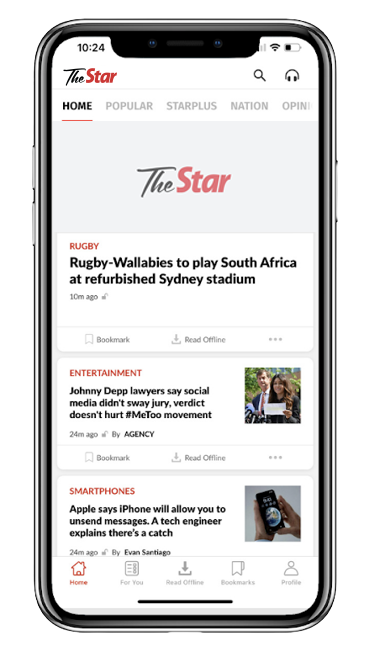
Cancel anytime. No ads. Auto-renewal. Unlimited access to the web and app. Personalised features. Members rewards.
Follow us on our official WhatsApp channel for breaking news alerts and key updates!