IN 1879, the French, buoyed by their success in building the Suez Canal, embarked on the construction of the Panama Canal in South America. Unfortunately, tens of thousands of workers died of various diseases, including malaria and yellow fever.
In 1904, the US bought all rights to the canal for US$40mil and began work. Within a year, workers began to succumb to yellow fever as well. However, times had changed and in 1900, US Army tropical disease expert Walter Reed proved that yellow fever was transmitted by the Stegomyia fasciata mosquito.
Win a prize this Mother's Day by subscribing to our annual plan now! T&C applies.
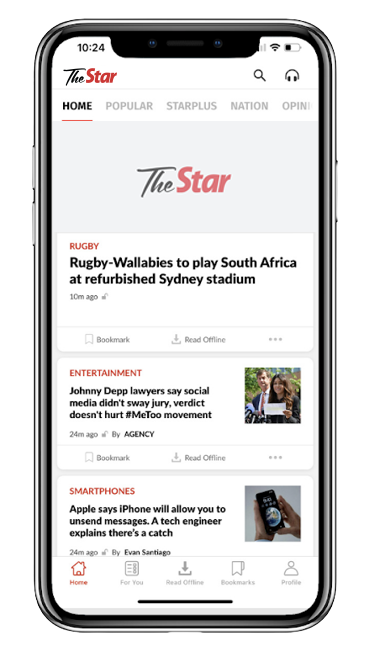